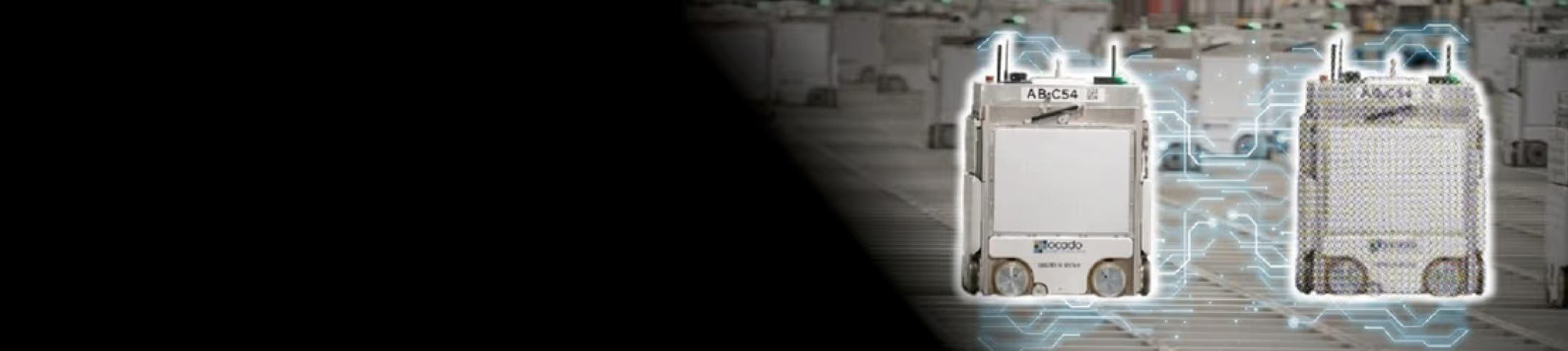
Digital twins
Our smart warehouses host complex robotics and automation ecosystems, and no two are the same. So, before we change the physical world, we simulate in the digital world, with our digital twins.
As we continue to scale facilities for our retail partners around the world, how can we go about making sure all elements of the built environment run seamlessly and at peak performance? How can we de-risk builds, anticipate issues and remove roadblocks, as well as spot ‘unknown unknowns’? With thousands of moving parts, how can we continue to innovate at speed?
We develop digital twin simulations to plan, prepare and optimise for various scenarios, such as hardware changes, in virtual worlds - before we make changes in real ones.
What is a digital twin simulation?
A digital twin is a digital replication of assets that mirrors the physical world. It is a virtual double of a physical asset, system, or process which allows companies to ask 'what if questions’ and provides accurate answers. This helps to optimise, run, and de-risk in more efficient ways, beyond human capabilities. A true digital twin optimises simulations in real-time, using real-world data, in a continuous circle.
We found existing simulation systems, even those used in automotive industries, weren't designed to cope with the number of moving parts and the complexity we had, so we built our own. We created our digital twin using precise software control, hundreds of algorithms, and millions of lines of code, all developed in-house.
We started with our pick aisles - creating models of our hardware, software, people, and communications systems to build a complete simulation. Every component was broken down, from our pick stations and pick locations to barcode readers. Then each component was added as a digital component to the simulation.
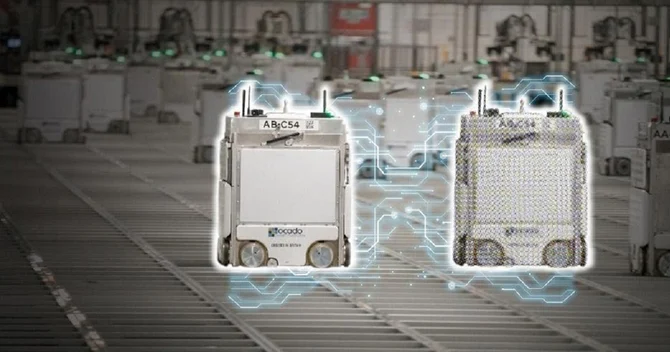
Adding real-world data to model behaviour
We want to account for real-world behaviour and variations in our pick stations as this approach will create a more reliable simulation. The team uses a broad range of simulation modelling techniques, including statistical modelling and real-world data sampling. We use real production data to understand the behaviour of hardware components rather than using the assumed behaviour. Then we model that behaviour for use in scenario testing, for example, to represent the process for the time taken to scan a barcode and even the rare possibility of that going wrong.
We also build-in tolerance errors. The team creates accurate statistical models for sources of possible variations. For example, the variation in the friction on conveyors which can cause the crates to slip slightly. By analysing a large amount of data, we can develop a distribution that predicts accurate results.
Decades of real-world testing in months
We feed data into our digital twin simulation to run 'what if’ scenarios. It runs in the same software as it would in production alongside the modelled hardware and people, which enables us to pose particular questions and gain complete insight into how the system behaves.
We iterate across pick station designs, to run hundreds of thousands of hours of digital twin simulations to understand which method is best. Thanks to our cloud-based computing cluster, thousands of simulations can be considered simultaneously, in the cloud, using machine learning to analyse the results.
Our production software is used in both the simulation and production, so the decisions made in the digital world are precisely those made in the physical world. This allows us to plan, prepare and optimise in the virtual world before building in the real one. We can run the equivalent of decades of real-world testing in just months within the virtual world.
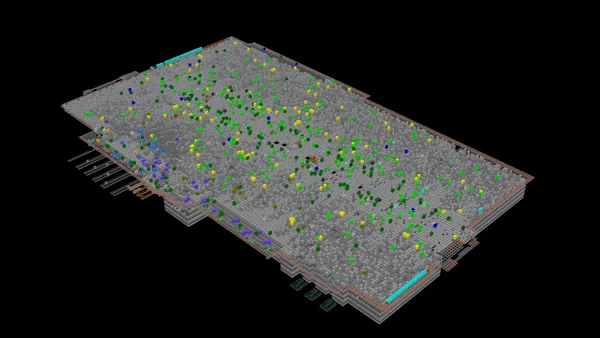
Monitoring and refining
We use simulations on our existing systems to test new features and integrations, as well as to monitor and refine factors such as those that could influence our pick stations’ performance.
Importantly, we feed this data and learnings back into the system to make positive change events. This means we continue to optimise simulations in real-time – using real-world data in a continuous circle, creating a true digital twin.
Evolving our digital twin
Today, our simulation has expanded way beyond our pick stations. Within our automated warehouses, our visualisation software allows us to create optimised grid layouts, develop algorithms to power our warehouses, test and analyse the performance of different warehouse configurations, and monitor live production systems.
It allows us to experiment with real-world questions such as ‘how do I design and optimise my entire site layout?’, ‘which hardware or software changes would impact most?’, or ‘what will my site cost?’ using the best outcomes to inform decisions.
Just the beginning
The use of simulations isn't limited to our automated warehouses. We've developed an expansive suite of simulation tools to model, test and optimise our systems.
Simulation models include our supply chain and ordering, which help us to forecast demand; our in-store fulfilment solution, which helps us optimise manual picking; and our vehicle routing, which helps us to determine optimal delivery routes.
Our vision is to develop our simulation capability to cover our operations end-to-end, from the webshop to the front door.
Automation and benefits beyond human capabilities
Today, accurately simulating such scenarios is a cornerstone feature of the Ocado Smart Platform, the end-to-end fulfilment, eCommerce, and logistics platform used by our international retail partners. Our simulations help our partners de-risk large investments and benefit from more resilient and predictable operations.
However, this powerful, applied AI can uncover efficiencies and new ways of doing things that otherwise would have remained out of sight. In the future, such simulations will help us evolve beyond what we already know, think, or can dream up, to help our retail partners achieve automation benefits at scale.
Change your world with us
Across Ocado Technology, we have a diverse, rich mix of teams and expertise working to solve complex problems. Learn more about our full range of opportunities here.