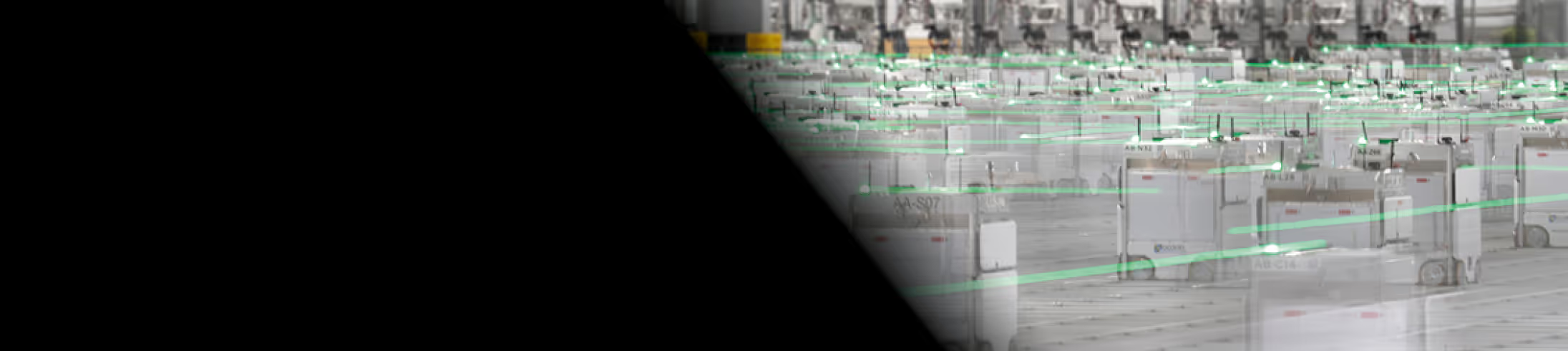
Hello, robot
Robust wireless communications are critical to the operation of our smart warehouses. This article explains our approach to ensuring we can talk to our bots anytime, anywhere.
In our automated warehouses, thousands of our bots operate in swarms to fulfil customer orders. Our bots travel at speeds of four metres a second, communicating ten times a second over wireless links. The bots travel over metal grids the equivalent size of several football pitches - sometimes working within a 150-metre radius.
Such factors present a complex set of challenges for wireless communications, as we need to communicate vast amounts of data quickly and reliably.
The Specialist
- Traditional wireless applications for warehouses and enterprise scenarios aren’t suitable for our Customer Fulfilment Centres (CFCs). Here are a few reasons why:
- Signals bounce off items in the environment, such as metal and concrete columns, walls and even bots.
- Signals have to travel across huge, indoor areas and wireless signal power decreases as the distance between the transmitter and receiver increases.
- Signals travel with limited vertical spacing.
- Building materials such as metal and even power inputs can impact the wireless link quality.
- Our environment is more dynamic than most radio propagation environments. For example, office environments might face obstructions from walls and people, but our CFCs face complex and reflective obstructions - such as thousands of bots moving at speed.
These elements combined could result in a drop off in signal variability and strength, degrading wireless communications. We call this problem the signal propagation phenomenon.
What’s more, each CFC is unique in its layout and design, according to our retail partners’ needs, so we need to factor in different grid sizes and the number of bots. Also, we need to operate reliably in other countries, under different regulations. With so many considerations, how do we reliably predict wireless link quality, anywhere in the world?
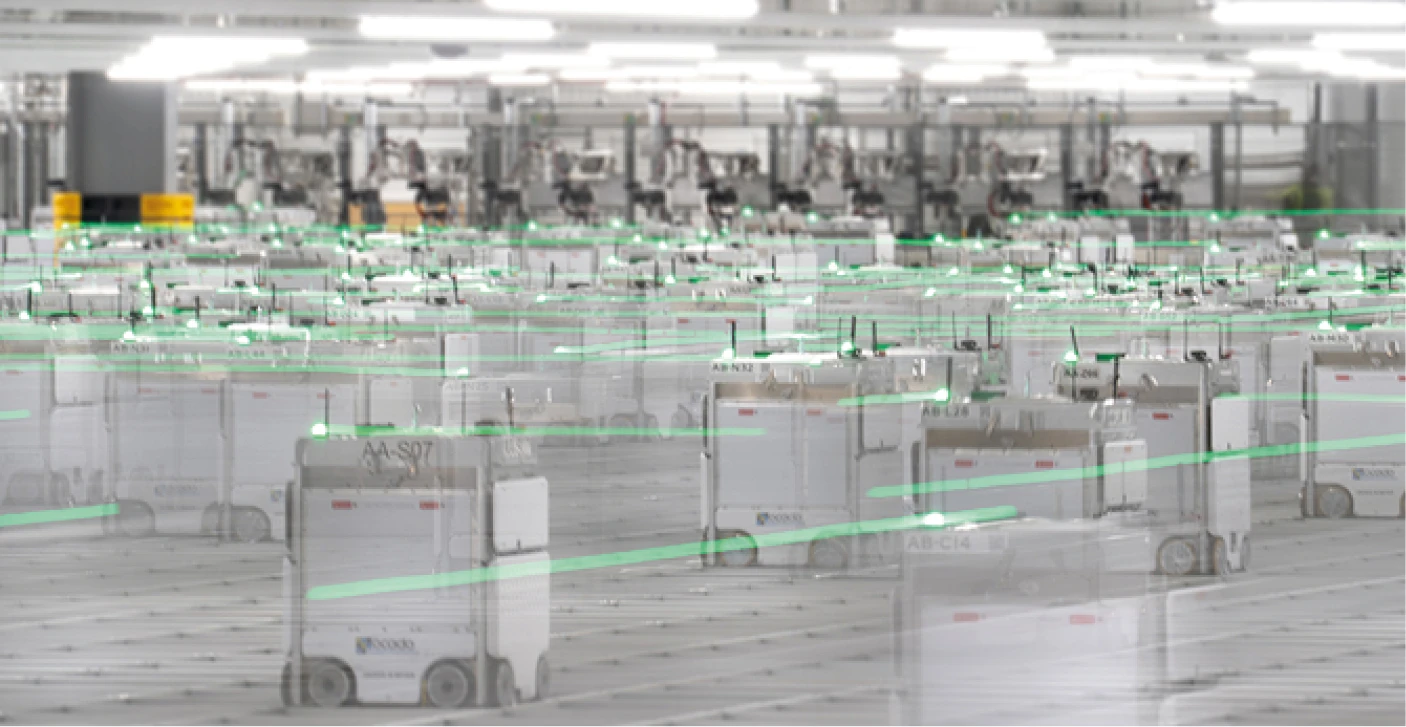
Modelling our wireless comms
Our models focus on the signal propagation phenomena (figure 1), analysing path-loss to predict the link quality between transmitters and receivers. In essence, lower path loss implies higher link quality, typically resulting in better reliability and performance.
We use an iterative approach to model signal propagation. This approach begins with selection of appropriate empirical models to form the basis of the project, which we then train and test using real-world data taken from over a million samples.
A tale of two models
Empirical or mathematical models are a good balance of complexity and accuracy. They are concise and relatively simple to put together as they only require a few variables (or factors such as distance and frequency).
We use two models for most use cases:
- Log-distance model. This is a classic path-loss model, commonly used for general wireless applications. It's relatively simple to put together as we only need to tune two parameters. The tuning is very accurate because the dataset is large.
- Two-segment model. This is less commonly used. Additional parameters are tuned when compared to the log distance model, which further improves accuracy.
We use the models for site selections and wireless designs in our warehouses - to reliably predict future wireless warehouse performance.
Training and testing
To train and improve our models for specific use cases, we use real-world path-loss data taken from our bots. This approach is unique because of the large dataset we use and the size of our automated warehouses.
Our data collection software is built in-house and runs 24/7 across our fleet of bots. The bot data is collected and uploaded to the cloud using our network infrastructure for further analysis.
Models are trained in one physical area and tested in another, so we can see how the model will generalise. What’s more, we continuously improve our models by constantly collecting new data.
Machine learning models
Looking to the future, we’re collating a large dataset to improve the accuracy of our models for new use cases. We do this by applying machine learning, and building a digital twin of our wireless communications.
This approach will allow us to accurately answer ‘what if?’ questions, which wouldn’t otherwise be possible with our empirical models, such as:
- What is the wireless power in a particular area of the CFC?
- What is the impact of the space between the grid and the ceiling?
- What is the effect of building materials on wireless quality?
- How do the layout of columns and even the movement of our bots impact wireless quality?
Using our models as a baseline, we can use machine learning to provide recommendations for the optimal parameters for wireless performance. Through this modelling we’ll be able to trial and optimise complex implementations in virtual worlds before building them in the real one.
We can continually improve these models, learning and refining them to achieve the best performance for each unique CFC. As a result, when it comes to deploying and maintaining wireless systems for our retail partners - we’ll get it right, the first time.
Change your world with us
Across Ocado Technology, we have a growing, diverse mix of data science teams helping us solve complex problems. Learn more about our full range of opportunities here.